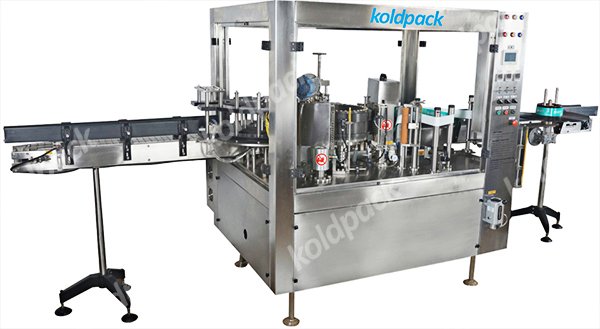
The Continuous Label Roll-Feed Labeling Machine is a fully automatic unit with electro-pneumatic controls for precise labeling. It features a base, label cutter, and glue assembly constructed from durable mild and alloy steels with a painted or hard chrome finish. The conveyor is made of S.S.304, while the chain is thermoplastic for reliable operation. Stainless steel shafts, column assemblies, and star housings ensure durability. Guides and stars are crafted from S.S.304, UHMWPE, and nylon. Enclosed in an S.S.304 frame with acrylic panels, the machine is operated via a Siemens PLC with a touch screen, and speed is managed by a Siemens Variable Frequency Drive for optimal performance and control.
Salient Features
- Simplifies label adjustments for precision cutting.
- Constructed from durable materials to minimize friction and static buildup.
- Modular design and quick-release change parts allow for fast and easy transitions between different containers or labels.
- Located at the drum's lower part and cutter, made from heat and wear-resistant materials for reliable performance.
- Adjusts the position of the I-MARK for accurate labelling.
- Ensures labels are only applied when bottles are present, reducing waste.
- Designed for hot melt labelling, accommodating various container sizes and round bottle shapes.
- Allows for quick and easy adjustments to different container sizes and labels.
Technical Specifications
Capacity | 120/150/200 BPM Smaller bottle/ label higher Speed Larger bottle/ label lower Speed |
Bottle (Diameter) | 50 mm Minimum, 105 mm Maximum |
Bottle height | 150 mm Minimum, 350 mm Maximum |
Label Width | 50 mm Minimum, 105 mm Maximum |
Label Length | 200 mm Minimum, 300 mm Maximum |
Label Placement from Base of Bottle to lower edge of label | 30 mm Minimum, 125 mm Maximum |
Label Roll Dimension | Maximum roll diameter 650mm Core diameter 75/76mm Unwind direction will be provided. |
Over all Dimension | Length : 1665 mm Width : 1175 mm Conveyor Length: 3 meter Infeed & Out feed Transfer extra |
Power Consumption | Main Motor : 2 HP Label Motor : 0.5 HP Conveyor motor : 0.75 HP Vaccum Pump Motor : 3 HP (Main Motor with Frequency Drive) |
Hotmelt Adhesive power | 3 KW |
Label Registration | By Danfoss control |
Label Control | By Print Mark sensor and Bottle sensor – both infrared Type |
Special Safety Features | 1) No bottle on conveyor, no delivery of label on drum 2) No label on drum, on adhesive application. |
Controllers | Controls by Hitachi Control. All Functionality indicated by Led. Complete electrical panel made in stainless steel. |
Hot melt Unit | Nordson unit |
Operation
The label roll is mounted on a rotary drum and guided through a track to the rotary label cutter assembly via a feed roller. The PLC system, using a color photocell to detect the “I” mark, precisely controls and cuts the label length. The label is then transferred to the vacuum drum using air pressure and vacuum systems, where it is securely held. As the drum rotates, the label’s edges are coated with hot melt glue from the glue drum, with glue pumped from the heating tank. Bottles are fed by a star wheel, rotated against the drum, and labeled using a roll-on press pad. The finished, labeled bottles are conveyed out of the machine. All functions are controlled by a PLC and electro-pneumatic systems for optimal performance.











Product Category
Primary packaging
– Rinsing for Mineral Water
– Filling for Mineral Water
– Capping for Mineral Water
– Rinsing For Juice
– Hot-Filling For Juice
– Capping For Juice
– Rinsing for Carbonated Soft Drinks
– Filling for Carbonated Soft Drinks
– Capping for Carbonated Soft Drinks
– Rotary Monoblock Glass Bottle Filling
– Linear Washing Filling For Glass Bottle
– Linear Washing capping For Glass Bottle
– Filling for Mineral Water
– Capping for Mineral Water
– Rinsing For Juice
– Hot-Filling For Juice
– Capping For Juice
– Rinsing for Carbonated Soft Drinks
– Filling for Carbonated Soft Drinks
– Capping for Carbonated Soft Drinks
– Rotary Monoblock Glass Bottle Filling
– Linear Washing Filling For Glass Bottle
– Linear Washing capping For Glass Bottle